Bioplastic, Meet Woody Biomass
Nordic Bioproducts Group and PTT MCC Biochem partner to add cellulose in bio-based plastic.
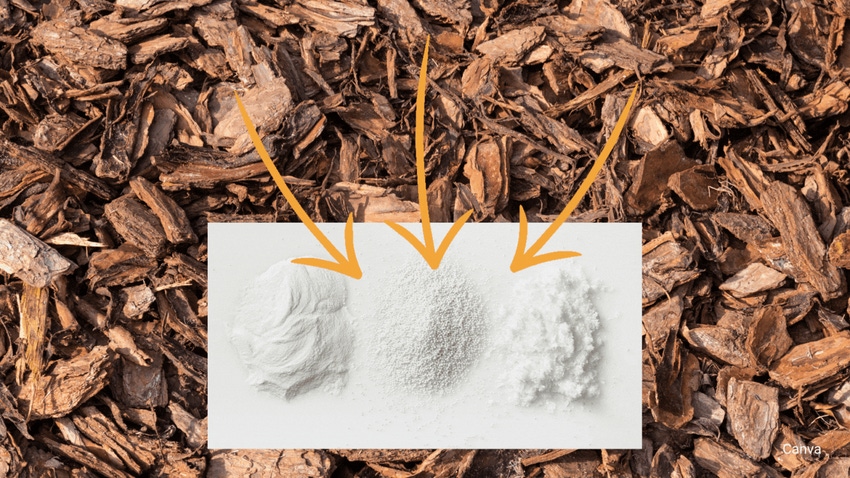
At a Glance
- Bioplastics will contain sustainable cellulosic materials.
- New grades of BioPBS will be home-compostable and biodegradable.
- Business arrangement features a biorefinery to process plantation residues.
Finnish startup Nordic Bioproducts Group (NBG) and Bangkok-based PTT MCC Biochem are partnering to develop bioplastic that incorporates cellulose. Target applications include single-use products made of conventional plastics.
The partnership focuses on new grades of bio-based polybutylene succinate (PBS) that incorporate NBG’s advanced, sustainable cellulosic materials, including activated cellulose fibers. The fibers can be used as a replacement for petroleum-based substances in the production of bioplastics.
NBG is a spin-off of Aalto University that specializes in cellulose innovation, bioproduct development, and commercialization. PTT MCC Biochem, a joint venture of PTT Global Chemical Public Company Limited and Mitsubishi Chemical Corp. (MCC), is a leading producer of biodegradable, compostable bio-based PBS, trade named BioPBS.
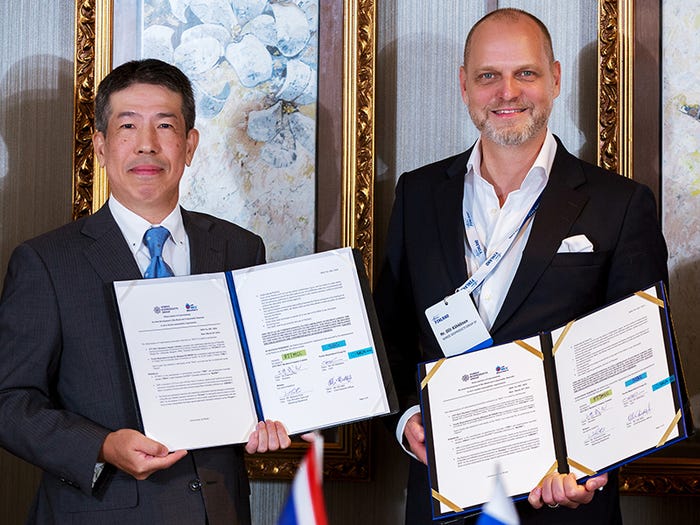
Mr. Takeyuki Doi, president of PTTMCC Biochem Ltd., and Olli Kähkönen, CEO and cofounder of NBG. NBG
Coffee capsules: A hot application.
The partners are aiming to develop high-performance, home-compostable bioplastics for production of single-use consumer products such as coffee capsules, cutlery, containers, plates, and mugs — items typically made from conventional, petroleum-based plastics.
Data from Allied Market Research indicate the coffee-capsule market alone will grow at a CAGR of 7.6% in the run-up to 2032, when it expected to reach a value of $11.9 billion. Many coffee-capsule formats are challenging to recycle because they incorporate non-residentially recyclable plastics or a combination of aluminum and plastic. Compostable capsules address that sustainability pain point.
BioPBS is food-contact approved in the United States, Europe, China, and Japan. NBG’s activated cellulose fibers also meet food-container safety regulations; the fibers are derived from clean water and Forest Stewardship Council (FSC)-certified, traceable, sustainably managed forests in Finland.
NBG’s collaboration with PTT MCC Biochem “represents a significant step forward in the green transition through innovative, high-performance, and environmentally friendly alternatives to traditional plastics. Bringing high-quality and competitive solutions to the market is key to making alternatives to plastic attractive and scalable,” says Olli Kähkönen, CEO and cofounder of NBG, in the memorandum of understanding (MOU) announcement.
Woody biomass to displace petrochemicals.
In January 2024, shortly before partnering with PTT MCC Biochem, NBG signed a separate MOU with Japanese multinational Marubeni.
NBG and Marubeni are collaborating to create a biorefinery that uses NBG’s lignocellulose-hydrolyzation technology, called AaltoCell. The venture, which aims to reduce dependence on fossil-based resources, will process woody biomass from Marubeni’s Indonesian plantations, including kraft pulp and plantation residues.
With NBG’s AaltoCell method, lignocellulosic materials are hydrolyzed — decomposed through a chemical reaction with water — to produce high-quality cellulose derivatives that can be used to produce pharmaceuticals and foods.
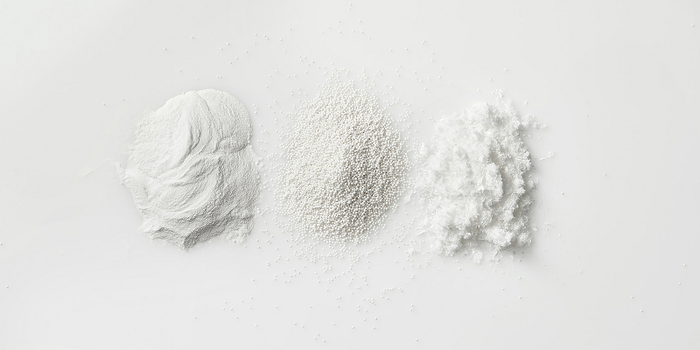
Close look at food-quality microcrystalline cellulose powders. NBG
The technology is environmentally friendly, with a smaller carbon footprint to produce resins and textiles vs. methods based on fossil fuels and chemical-intensive processes. An independent third-party assessment indicates the AaltoCell technology can reduce the carbon footprint of cellulose-derivative production by 80% vs. conventional methods.
“We are delighted that big companies like Marubeni and PTT MCC have trusted us and our technology to help them achieve their ambitious goals,” Kähkönen said. “As we are gearing towards impact at scale and mass production, we can be a vital partner for more and more big, global companies, helping them create environmentally conscious products that meet the highest standards of quality and sustainability.”
World’s first for microcrystalline cellulose production.
NBG continues to expand its technology. The company announced April 24 the opening of its commercial-scale production facility for microcrystalline cellulose and other cellulose derivatives in Lappeenranta, Finland. The new factory features the world's first continuous production line of up to 10,000 tons of high purity microcrystalline cellulose annually. It employs 20 and plans to double that number soon.
Sustainability in the facility’s production practices is also a priority. It anticipates producing zero solid waste and using only a fraction of the chemicals, water, and electricity compared to traditional MCC production processes.
The factory is expected to create 40 million euros (about $42.8M) in revenue in the first full operating year, aiming to triple revenue in three years.
With full production capacity now operational, NBG is poised to welcome additional clients from various industries and countries for several product markets, especially bioplastics.
Microcrystalline cellulose has been used in a range of industries for decades from pharmaceuticals and food supplements to food ingredients, cosmetics, and skincare.
About the Author(s)
You May Also Like